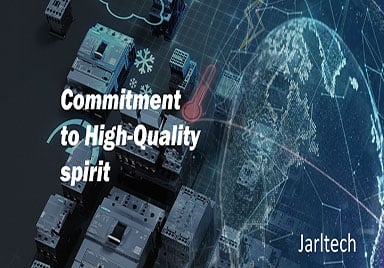
Quality Management
Commitment to a High Standard of Excellence
In today's rapidly evolving market, electronics manufacturers are facing a number of challenges, including:
.Growing global competition
.It is imperative that we deliver top-quality products.
.An ongoing necessity to reduce costs
.Supplies sourced from around the globe
In light of these challenges, quality managers in the electronics industry must have real-time visibility—both within facilities and worldwide—to enable proactive measures.
.Maximize efficiency and output.
.Reduce expenses
.Decrease waste and scrap
.Continuous improvement is the key to enhancing processes.
.Ensure the traceability of parts and products.
.Quality Control Solutions for the Electronics Industry
Our extensive knowledge base allows us to assist you in overcoming critical quality control challenges in the electronics field.
Quality Control Procedure
At Jarltech, quality is not just an attitude; it is a carefully structured system. Our engineers and operators implement rigorous quality control measures through comprehensive documentation and procedures at every production stage. The quality control process comprises three distinct phases, each overseen by a specialist. Furthermore, the system includes redundancy to ensure that no quality issue is overlooked.
Incoming Quality Control
The IQC process is responsible for conducting inspections and addressing quality issues prior to the commencement of assembly. Furthermore, it assists suppliers in maintaining quality control for raw materials and semi-finished products (modules) to guarantee incoming quality and prevent the use of defective components.
The IQC is responsible for the following tasks
1. Conduct a check of the approved vendor list.
2. Carry out a verification of the approved vendor list.
3. Conduct a quality assessment of the supplier records.
4. Incoming materials must be sampled in accordance with the requirements set forth in the MIL-STD-105E standard.
5. Perform dimensional, visual, and functional inspections of material samples.
6. Track the quality control chart for inspected properties and notify the engineering team of any significant deviations.
7. The IQC process will be continuously improved.
In-Process Quality Control
Our IPQC process oversees our quality systems throughout the assembly process, ensuring that any issues that may arise are identified and addressed in a timely manner.
The IPQC is responsible for the following key tasks
1. Inspect assembled and in-process materials in accordance with IPC-A-610D standards.
2. Perform both automated and manual in-line inspections (for further details, please refer to our Testing Equipment page).
3. Following the setup of the process, a first-article inspection should be carried out.
4. Use statistical control techniques and monitor for significant deviations.
5. Conduct audits of ongoing processes to verify compliance with standards and identify areas for improvement.
Outgoing Quality Assurance (OQA) is the final step before products are shipped to customers. It is essential to ensure that our shipments are error-free and meet the highest quality standards.
Before shipment, our OQC department rigorously conducts essential inspections and tests according to specifications to ensure the overall quality of production. The finished product is then placed on a fumigated wooden pallet and covered with a waterproof bag to protect it from moisture during transportation.
OQA's responsibilities include
The OQA process is the final quality control step before products are shipped to customers. Ensuring that our shipments are defect-free is a critical aspect of this process. To ensure the effectiveness of earlier processes, several redundancies with IQC and IPQC are implemented.
Prior to production dispatch, our OQC department will conduct the requisite examinations and tests in accordance with the Inspection Specification, thereby ensuring product quality. Finished goods will be placed on fumigated wooden pallets and covered with waterproof bags to prevent moisture ingress during transportation.
The primary responsibilities of the OQA include
1. Conduct visual and functional inspections.
2. Validate the first-article inspection.
3. Recheck the approved vendor list.
4. Implement sampling in accordance with the MIL-STD-105E standard.
5. Perform reliability testing.
6. Submit failure analysis reports and notify the engineering team.
Fully Equipped Test Equipment
Our product testing process is comprehensive, ensuring that each product meets our clients' final requirements. Jarltech utilizes a variety of testing equipment for assembly lines. Based on customer requirements throughout the manufacturing process, we have multiple test stations equipped with specific functional tests to conduct thorough quality checks.
Furthermore, we offer warranty and repair services, including ECO upgrades (hardware and software), system-level repairs, and component-level repairs. Each repair project includes a comprehensive engineering failure diagnosis and an in-depth root cause analysis. All repair work is conducted in a clean, static-free environment to ensure the highest quality standards are met.
Production Procedures
Production Procedures: A manufacturing process is a dynamic system with evolving structures,...
DetailsQuality Management | Cutting-Edge POS Systems Manufacturer | Jarltech
Located in Taiwan since 1987, Jarltech International Inc. has been a developer and manufacturer of POS and Kiosk systems for restaurants, retail stores and supermarkets. Their main software and hardware products include, Quality Management, small business POS systems, self-service kiosks, smart card readers, Bluetooth thermal printers, embedded motherboards and all-in-one panel PCs, focusing on providing interactive kiosk solutions.
Leverage Jarltech’s 30+ years of expertise in developing innovative POS and Kiosk systems tailored for diverse business needs in restaurants, retail stores, and supermarkets. Our specialized solutions, encompassing IPC, Touch Monitor, Thermal Printer, and Smart Card Reader, are designed to elevate your business operations, ensuring seamless transactions and enhanced customer experiences.
Jarltech has been offering customers global B2B solutions with Jarltech’s POS and Kiosk Systems since 1987, both with advanced technology and 37 years of experience, Jarltech ensures each customer's demands are met.